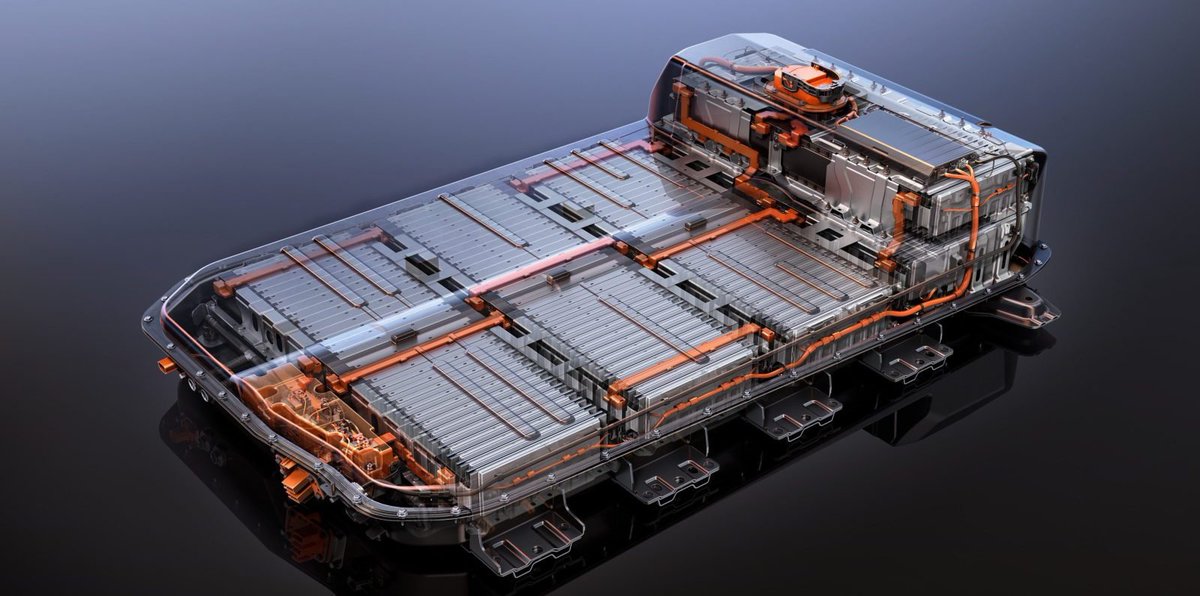
EV Battery overview
Batteries are the key differentiator between the various EV manufacturers. The amount of energy stored in the battery determines the range of the EV, thought to be a major limitation on EV sales.
Batteries are the key differentiator between the various EV manufacturers. The amount of energy stored in the battery determines the range of the EV, thought to be a major limitation on EV sales.
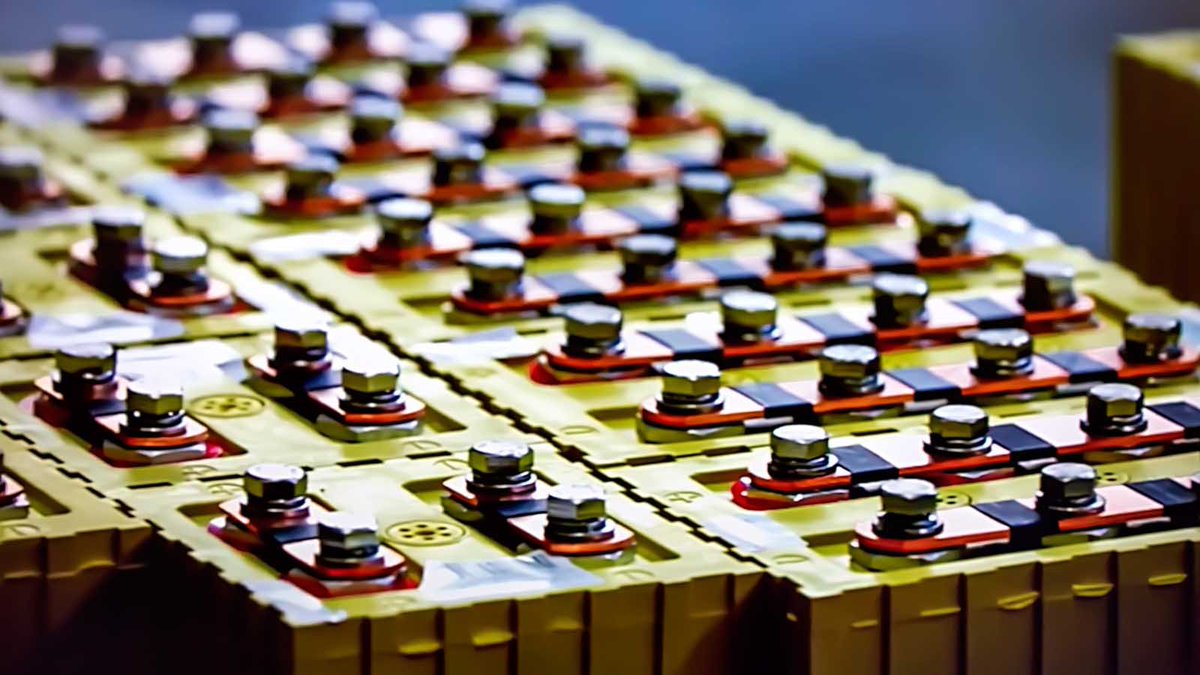
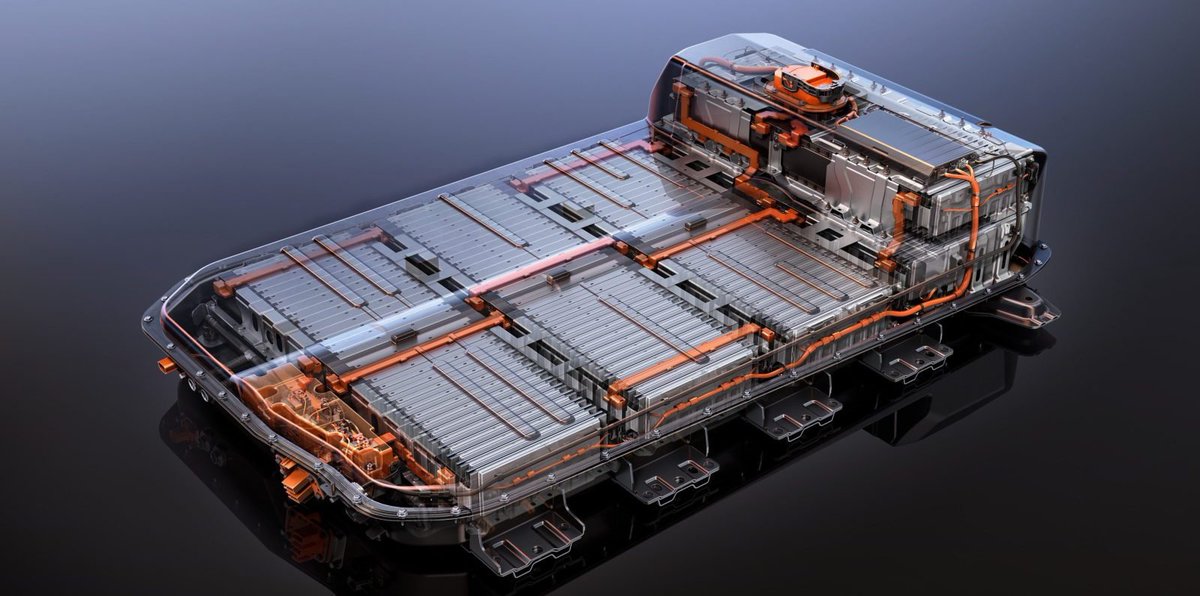
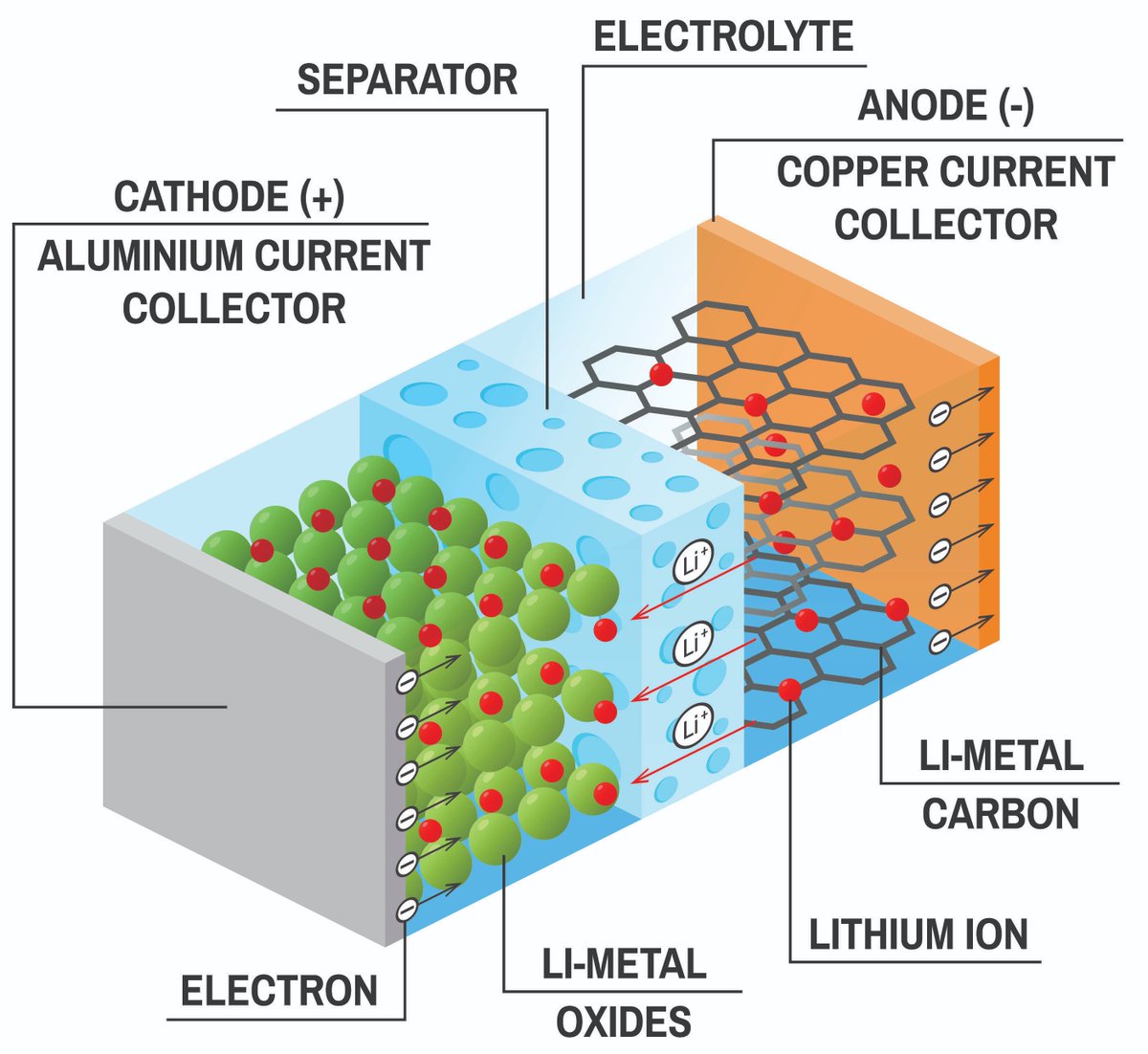
BNEF projects that global production capacity for lithium-ion batteries will increase from 103 gigawatt-hours (GWh) in the first quarter of 2017 to 273 GWh by 2021.
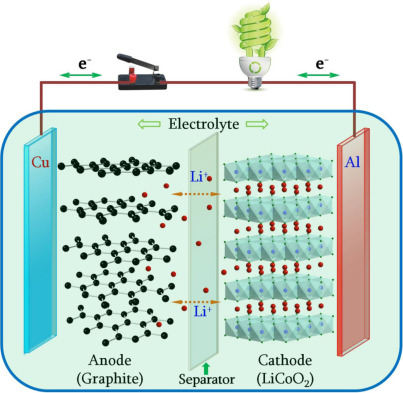
cell manufacturing,
module manufacturing, and
pack assembly.
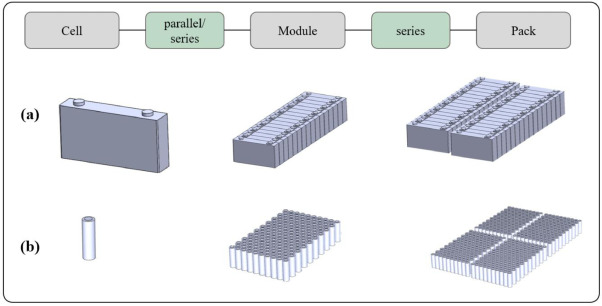
electrochemical cell,
which consists of three major parts: a cathode and an anode separated physically but connected electrically by an electrolyte.
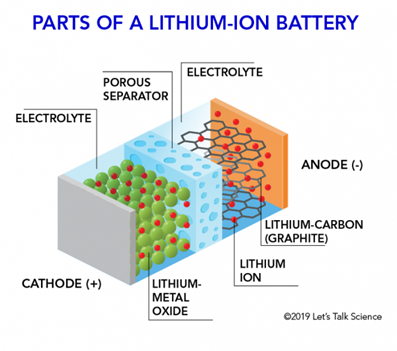
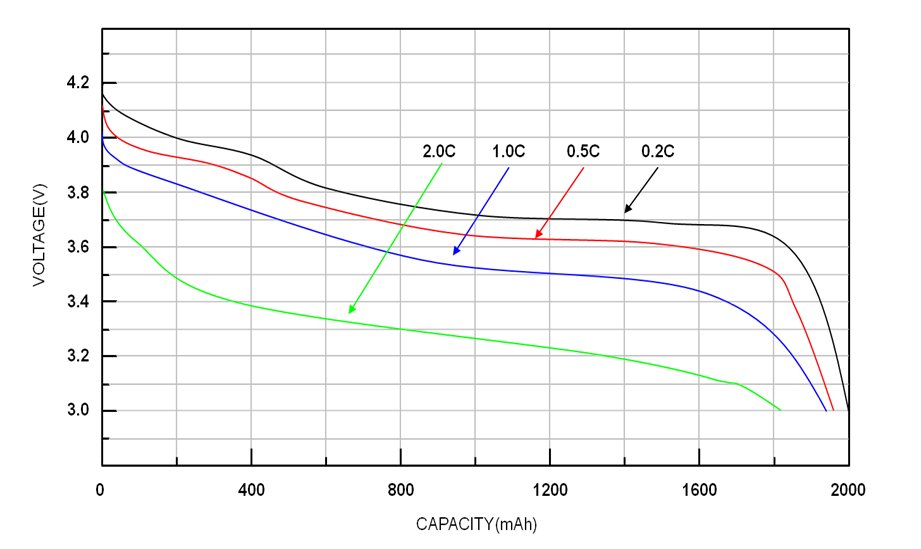
Tesla’s battery packs use cells from Gigafactory, while cells for the Model S & X are produced by Panasonic
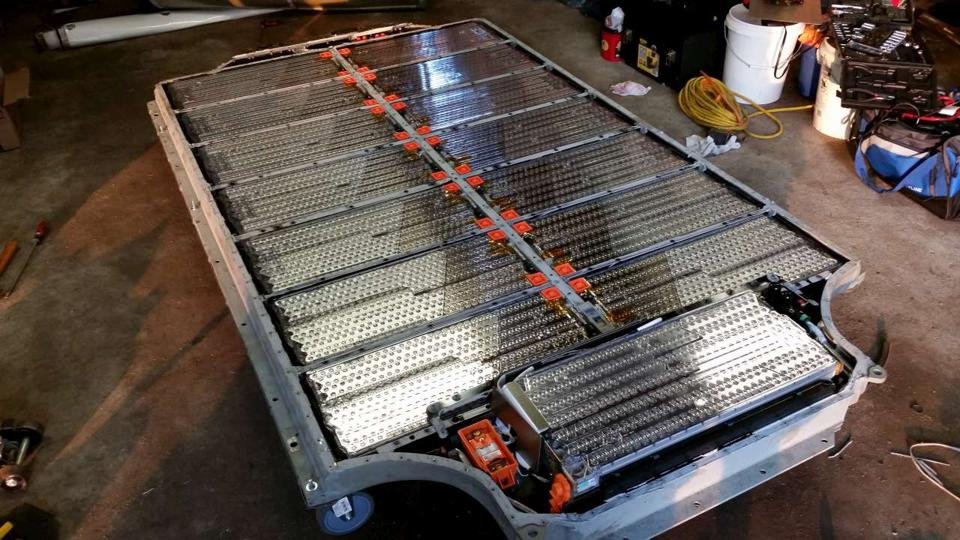
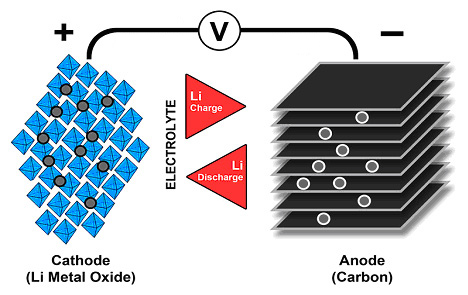
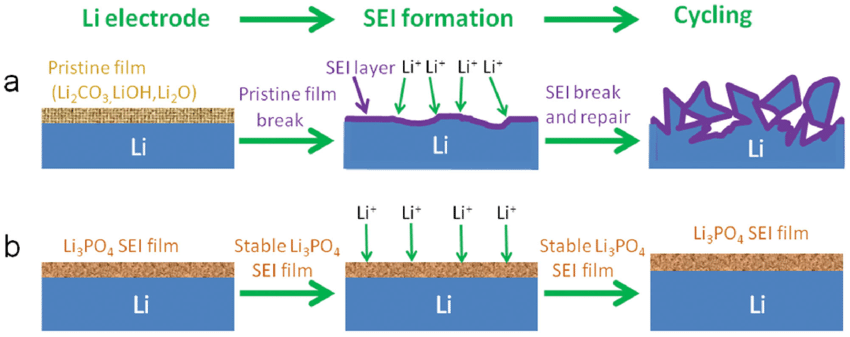
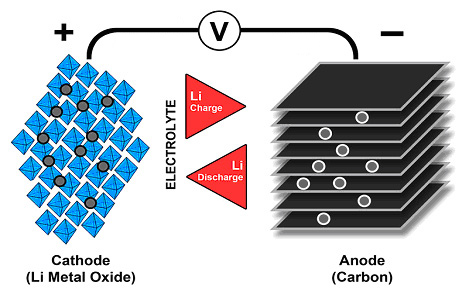
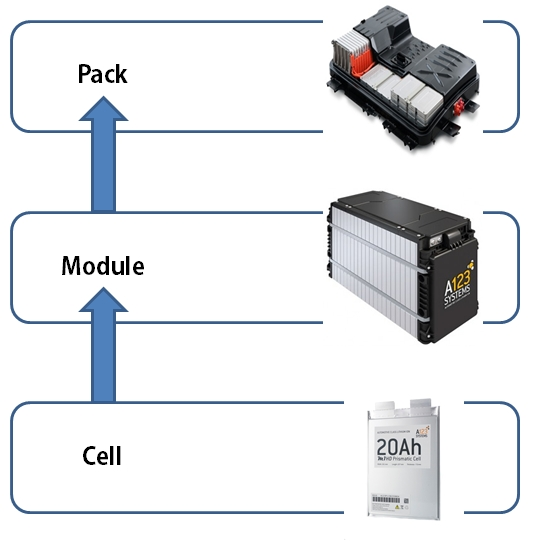

Graphite is used in the anode of many EVs.
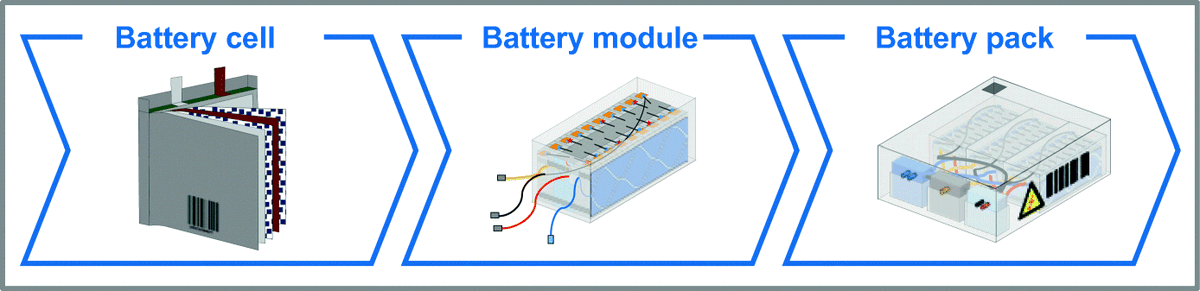

$TSLA is aiming to reduce the cost of future packs to less than $6,000, which would put the cell cost at well under $100/kWh.
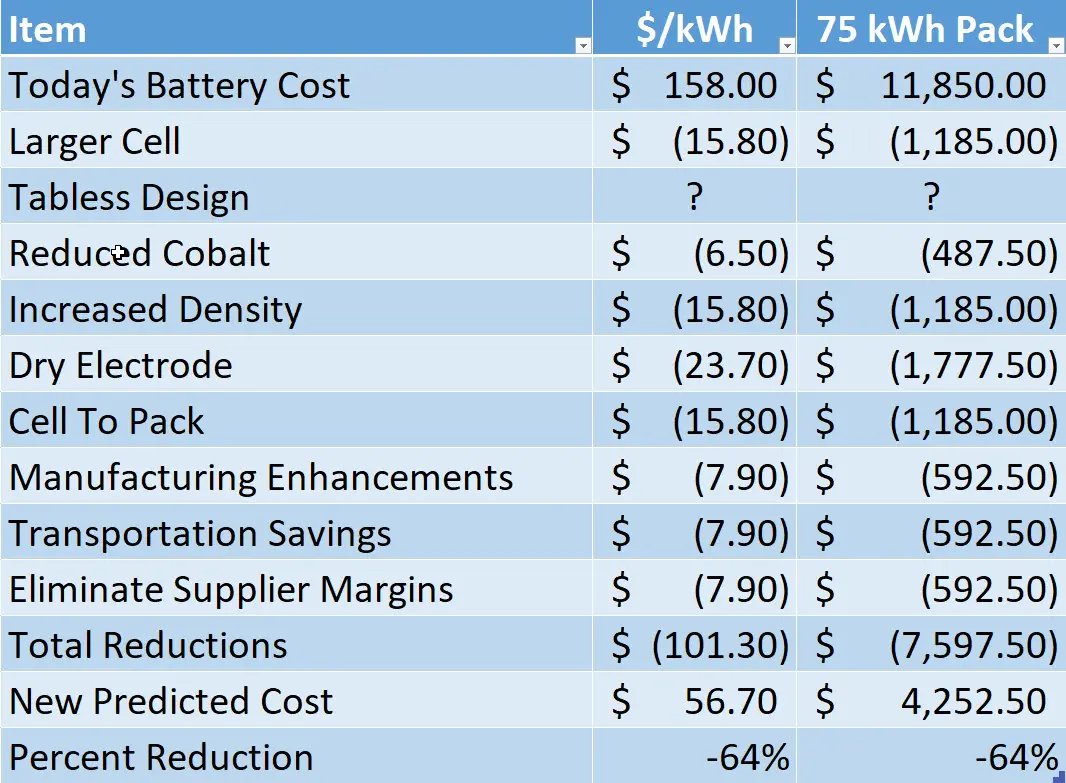
More from Tech
After getting good feedback on yesterday's thread on #routemobile I think it is logical to do a bit in-depth technical study. Place #twilio at center, keep #routemobile & #tanla at the periphery & see who is each placed.
This thread is inspired by one of the articles I read on the-ken about #postman API & how they are transforming & expediting software product delivery & consumption, leading to enhanced developer productivity.
We all know that #Twilio offers host of APIs that can be readily used for faster integration by anyone who wants to have communication capabilities. Before we move ahead, let's get a few things cleared out.
Can anyone build the programming capability to process payments or communication capabilities? Yes, but will they, the answer is NO. Companies prefer to consume APIs offered by likes of #Stripe #twilio #Shopify #razorpay etc.
This offers two benefits - faster time to market, of course that means no need to re-invent the wheel + not worrying of compliance around payment process or communication regulations. This makes entire ecosystem extremely agile
So I have been studying this entire communication layer as its relevance is ever growing with more devices coming online, staying connected, and relying on real-time communication. Not that this domain under penetrated, but there is a change underway.
— Ameya (@Finstor85) February 10, 2021
This thread is inspired by one of the articles I read on the-ken about #postman API & how they are transforming & expediting software product delivery & consumption, leading to enhanced developer productivity.
We all know that #Twilio offers host of APIs that can be readily used for faster integration by anyone who wants to have communication capabilities. Before we move ahead, let's get a few things cleared out.
Can anyone build the programming capability to process payments or communication capabilities? Yes, but will they, the answer is NO. Companies prefer to consume APIs offered by likes of #Stripe #twilio #Shopify #razorpay etc.
This offers two benefits - faster time to market, of course that means no need to re-invent the wheel + not worrying of compliance around payment process or communication regulations. This makes entire ecosystem extremely agile